Ohne Photovoltaik gibt es keine Energiewende – diese Einsicht hat sich mittlerweile auch im letzten Winkel der Bundesrepublik herumgesprochen. Doch die Umwandlung von Sonnenlicht in Strom ist nicht die einzige Technologie aus der Welt der Photonik, die uns beim klimagerechten Umbau der Wirtschaft wertvolle Dienste leisten wird. „Photonik kann dazu beitragen, den weltweiten CO2-Ausstoß um drei Milliarden Tonnen zu mindern“, sagt Prof. Stefan Kaierle, Vorstandschef des Laserzentrums Hannover (LZH). Das entspricht etwa elf Prozent des Zielwertes aus dem Pariser Klimaschutzabkommen.
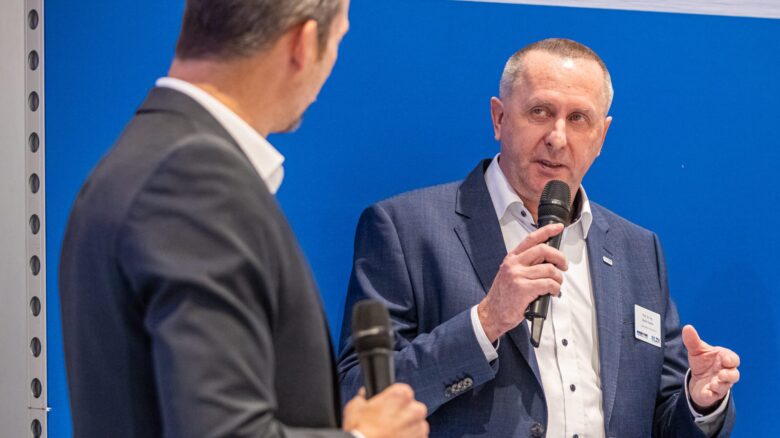
Neben dem Solarstrom spielt dabei vor allem der Einsatz von optischen Lösungen im Datenverkehr eine zentrale Rolle: Photonische Schaltkreise in den Rechenzentren dieser Welt und Glasfaserkabel verhindern, dass der gigantische Energieverbrauch durch den „Stromfresser Internet“ noch weiter durch die Decke schießt. Zum weltweiten Klimaschutz tragen aber auch energieeffiziente Displays und Beleuchtung, neue Recyclingmöglichkeiten durch Lasertechnologie oder Materialeinsparungen mithilfe von 3D-Druck bei. Insbesondere in der sogenannten „additiven Fertigung“, bei der Schicht für Schicht dünne Materiallagen aufgetragen und zu dreidimensionalen Gegenständen zusammengefügt werden, schlummern noch riesige Nachhaltigkeitspotenziale. Und ganz nebenbei findet in vielen Produktionsbereichen eine kleine industrielle Revolution statt.
Die hannoversche Goldschmiede Stichnoth hat die Vorteile des 3D-Drucks schon vor fast zehn Jahren erkannt. Sonderanfertigungen wie Trauringe, Antragsschmuck oder Colliers werden bei dem mittelständischen Handwerksbetrieb inzwischen am Computer designt. Ein 3D-Drucker erstellt daraus dann eine Wachsform, die später für den Guss des Schmuckstücks verwendet wird. „Das erleichtert uns die Arbeit sehr, weil man das normalerweise per Hand modellieren müsste. Wir lassen die Drucker über Nacht laufen und dann müssen wir nur noch gießen“, berichtet Florian Stichnoth beim Innovationstag im Laserzentrum.
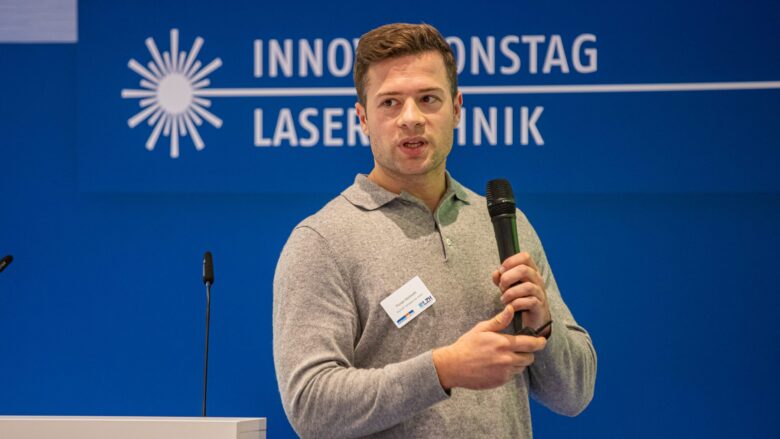
Auch für die Lasergravur ist eine Maschine zuständig, Edelsteine müssen aber nach wie vor per Hand eingesetzt werden. Für die Herstellung eines Solitärrings benötigt der 3D-Drucker etwa 12 Stunden. „Man kann das aber noch feiner einstellen, dann dauert der Druck bis zu 40 Stunden“, sagt der gelernte Goldschmiedegeselle und studierte Betriebswirt. Das Schmuckdesign am PC hat auch den Vorteil, dass die Kunden anhand eines 3D-Renderings abschätzen können, ob ihnen das Produkt am Ende auch gefallen wird.
„Wo man sonst zwei bis drei Wochen benötigte, schaffen wir das nun innerhalb einer Woche“, nennt Stichnoth den größten Vorteil des modernen Herstellungsverfahrens. Theoretisch könnte sich die Goldschmiede sogar den Guss sparen und die Schmuckstücke direkt vom 3D-Drucker anfertigen lassen. Das würde beim Design mehr Spielräume eröffnen, durch das Drucken und Fräsen aber auch zu mehr Materialverlust und höheren Herstellungskosten führen. Außerdem sprechen logistische Gründe gegen diesen Schritt. „Für den Pulverdruck braucht man relativ große Materialbehälter, deswegen tun wir uns da ein bisschen schwer“, sagt Stichnoth.
Bei der Firma EOS herrscht bereits totale Designfreiheit. Egal ob Fuß-Orthesen für Ottobock, ICE-Bauteile für die Deutsche Bahn, Raketenantriebe für das Ariane-Programm oder Hunde-Duschbrausen für Hansgrohe – der bayerische Industriepionier kennt bei der additiven Fertigung keine Grenzen. Für die 3D-gedruckten Brillen des jungen Unternehmens „You Mawo“ hat sich EOS vom Fraunhofer-Institut die Umweltvorteile einmal ausrechnen lassen: Während die Standard-Brille vom Innenstadt-Optiker auf durchschnittlich 7,23 Kilogramm CO2 kommt, liegt die online bestellte 3D-Brille bei nur 3,06 Kilogramm CO2 – über den gesamten Lebenszyklus hinweg betrachtet.
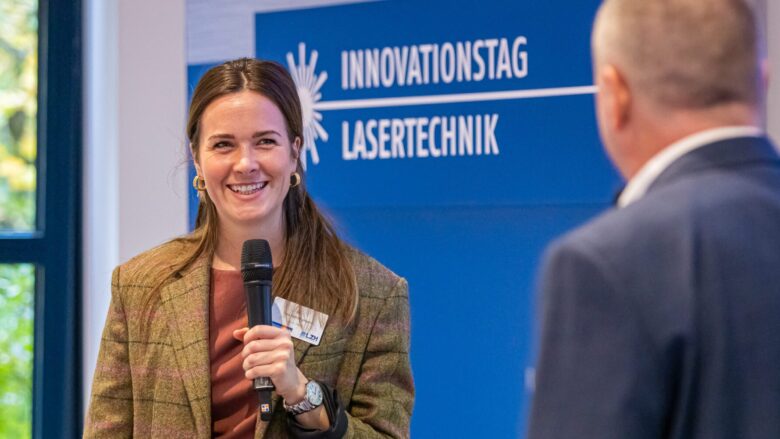
Der große Unterschied sei zum einen auf das ressourcenschonende Herstellungsverfahren zurückzuführen. Zum anderen hänge das damit zusammen, dass viele Hersteller von konventionellen Acetatbrillen mittlerweile nach China abgewandert sind, erklärt Tina Schlingmann, EOS-Regionaldirektorin im deutschsprachigen Europa. „Der Transport ist einer der Faktoren mit dem höchsten Impact auf den CO2-Fußabdruck“, sagt die promovierte Wertstoffwissenschaftlerin, die als Fertigungschefin bei der Deutschen Bahn auf 3D-Druck gesetzt hat. In ihrer Zukunftsvision gibt es keine überfüllten Warenlager mehr, wo nicht genutzte Ersatzzeile irgendwann verschrottet werden. „Die ideale Welt sieht so aus: Wir haben ein digitales Warenlager und drucken nur noch das Gerät, das wir benötigen.“
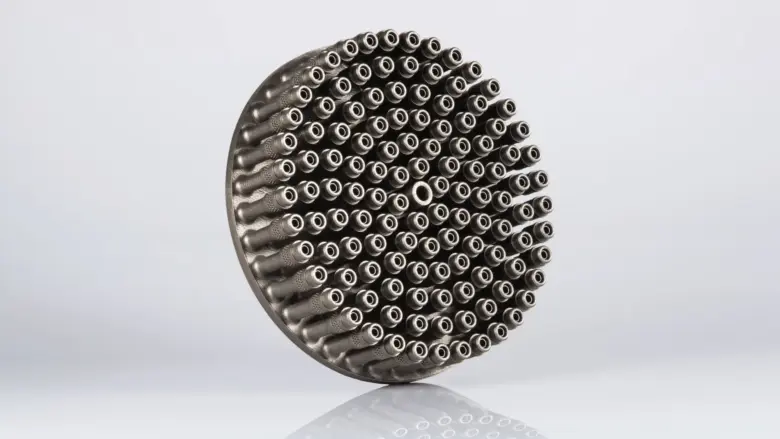
Gleichzeitig erforscht ihr Unternehmen nachhaltigere Kunststoffe für den industriellen 3D-Druck. „EOS hat ein klimaneutrales Polymer auf Basis einer Rizinusbohne entwickelt“, verrät Schlingmann. Bei der Produktion des biobasierten Materials fallen kaum noch CO2-Emissionen an, die volle Klimaneutralität werde über Kompensationsmaßnahmen erzielt. Nun geht es nur noch darum, dass davon auch die Kunden profitieren. „Wir schaffen zurzeit unsere eigenen Standards, die von außen zertifiziert werden“, berichtet Schlingmann und verweist auf eine Zusammenarbeit mit TÜV Süd und Fraunhofer. Auf dieser Grundlage stellt dann auch EOS seinen Kunden Zertifikate aus, die diese dann in ihren Nachhaltigkeitsbericht aufnehmen können.
Auf die Entwicklung von hocheffizienten Sensoren, die ebenfalls auf Photonik beruhen, hat sich die Firma „4D Photonics“ aus Isernhagen (Region Hannover) spezialisiert. „Wir haben einen Sensor, mit dem man wirklich alle Anwendungen erschlagen kann und der über Software vollkommen konfigurierbar ist“, sagt Geschäftsführer Christoph Franz. Das Gerät namens „Weld-Watcher“ (Weld ist Englisch für Schweißen) kommt bei der automatisierten Überwachung des Laserschneidens oder Laserschweißens zum Einsatz, um die Effizienz zu verbessern und den Ausschuss durch Produktionsfehler zu reduzieren.
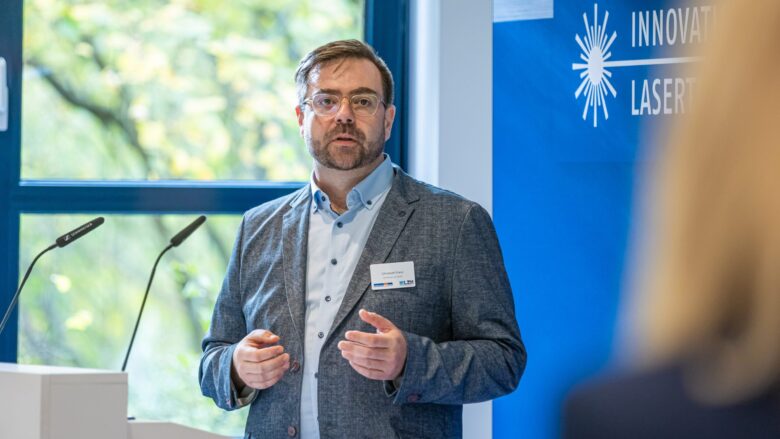
Die Einsatzbereiche liegen laut Franz in der Batteriezellenproduktion, im 3D-Druck, in der E-Mobilität oder in der Wasserstofftechnik. Ein neues Geschäftsfeld hat sich aufgrund der neuen Euro-7-Abgasnorm aufgetan. „Die Hersteller sind aufgefordert, Bremsscheiben herzustellen, die deutlich weniger Feinstaub emittieren“, erklärt Franz. Bei der Beschichtung dieser Bremsscheiben kommt Hochgeschwindigkeits-Lasertechnologie zum Einsatz, die fehleranfällig ist und überwacht werden muss. „Wir fahren gerade die Stückzahlen für die dazugehörigen Sensoren hoch“, berichtet der Unternehmer.
„Viele mittelständische Industriebetriebe aus Niedersachsen sind als ‚Hidden Champions‘ in Marktnischen unterwegs, für die sie industrienahe Forschung und das Laserzentrum brauchen“, weiß Volker Schmidt, Hauptgeschäftsführer von Niedersachsen-Metall und Vorsitzender des LZH-Industriebeirats. In Maschinenbau, Medizintechnik und Automotive-Bereich stelle das interdisziplinäre Photonik-Forschungszentrum ebenso wie das Institut für Integrierte Produktion (IPH) und das Deutsche Institut für Kautschuktechnologie (DIK) einen „unschätzbar wichtigen Partner“ dar. „Diese Forschung ist entscheidend dafür, ob wir mit Innovationen aufwarten können“, betont Schmidt.
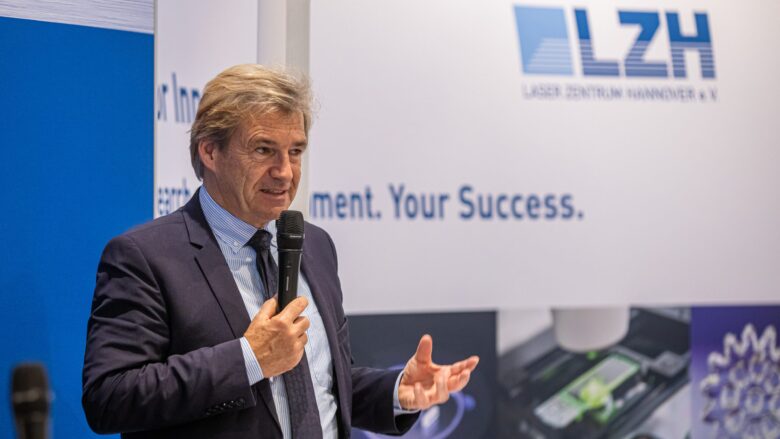
Bei der Fähigkeit, innovative Produkte und Dienstleistungen zu entwickeln, fällt Deutschland allerdings immer weiter zurück. Laut dem jüngsten BDI-Innovations-Indikator liegt die Bundesrepublik nur noch auf Platz 10 von 35 Volkswirtschaften. Deutschland investiert zu wenig und zu langsam in neue Trends, sagen die Studienautoren vom Fraunhofer-Institut für System- und Innovationsforschung (ISI) und dem Leibniz-Zentrum für Europäische Wirtschaftsforschung (ZEW).
„Umso wichtiger ist es, dass die wirtschaftlichen Rahmenbedingungen am Standort Deutschland endlich so verbessert werden, dass unsere Unternehmen diesen Vorteil im internationalen Wettbewerb auch wieder ausspielen können. Andernfalls verlieren wir mittelfristig den Status als Land der Spitzentechnologie und gefährden unseren Wohlstand“, sagt Niedersachsen-Metall-Hauptgeschäftsführer Schmidt.
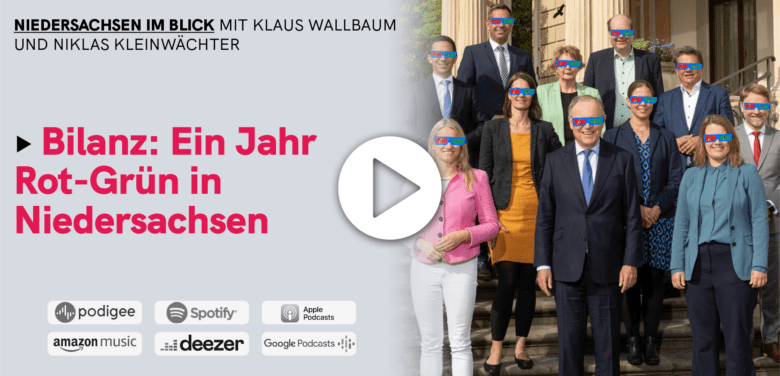