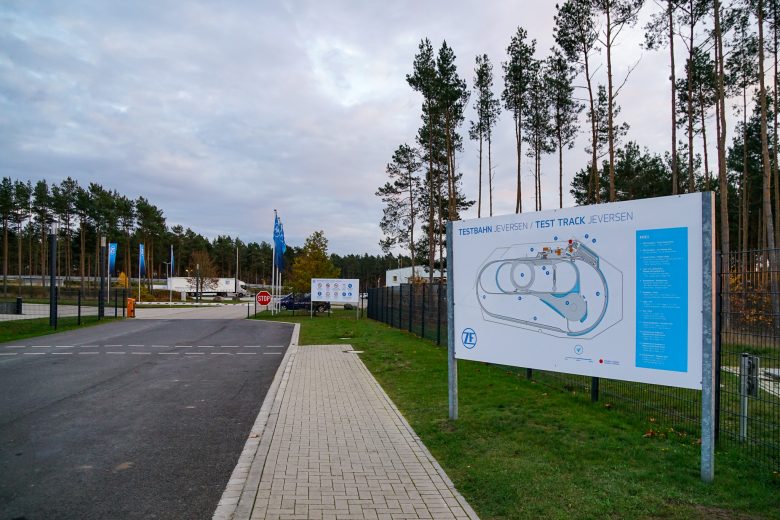
Auf seinem Testgelände im Landkreis Celle bastelt der Automobilzulieferer ZF an einer kleinen Revolution des Güterstraßenverkehrs. Nachdem die Elektrifizierung von Lastwagen noch in weiter Ferne scheint, hat das auf Antriebs- und Fahrwerktechnik spezialisierte Unternehmen eine Alternative gefunden, die sich schneller und einfacher umsetzen lässt: Mit dem der Hightech-Anhänger „E-Trailer“ wird jeder konventionelle Lastwagen zu einem Hybrid-Fahrzeug. Anstatt die Zugmaschine auf E-Mobilität umzurüsten, stecken die ZF-Entwickler einen Elektromotor in den Auflieger und zapfen dessen Bewegungsenergie als Stromquelle an. „Rekuperation“ heißt das im Fachjargon und beschreibt die Rückgewinnung von Energie, die ansonsten verloren gehen würde.
„40 Tonnen haben eine irre kinetische Energie. Wenn ich diesen Strom in die Reibbremse packe, verpufft er einfach. Wir wollen aber möglichst alles wieder einsammeln“, erklärt ZF-Entwicklungsingenieur Dirk Hillbring. Die dadurch eingesammelte Energie wird in einer Batterie gespeichert und kann dann für den Fahrzeugantrieb wiederverwendet werden. Nach internen Messungen werden durch das hybride Energie-Recycling auf Kurzstrecken bis zu 16 Prozent Kraftstoff eingespart, bei Langstrecken sind es immerhin noch 7 Prozent. Die CO2-Reduktion pro Fahrzeug liegt laut ZF bei bis zu 15 Tonnen pro Jahr. „Wenn ich nur geradeaus fahre und wenig bremse, verliert sich das natürlich“, sagt Hillbring. Sein volles Potenzial entfalte der E-Trailer deswegen auch eher beim Lieferverkehr für Supermärkte und Discounter oder ähnlichen Fahrten für den Einzelhandel.
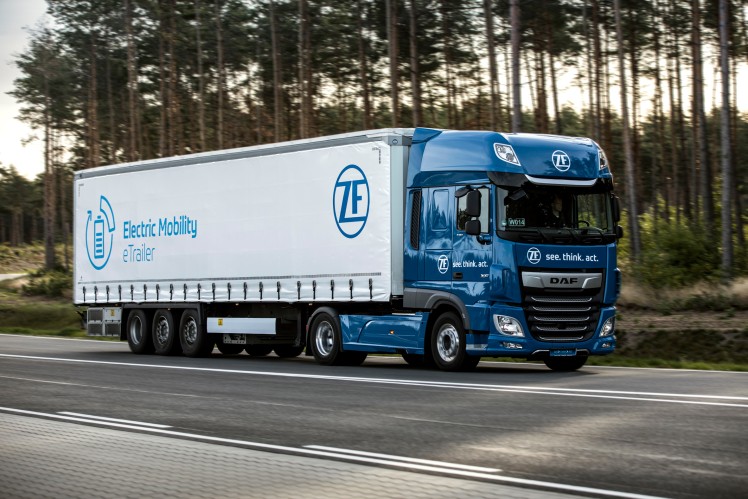
Bei der Probefahrt mit dem Prototyp läuft der E-Trailer zwar scheinbar einwandfrei. Über ein Touchpad kann Hillbring sogar während der Fahrt den gesamten Prozess der Rekuperation steuern und individualisieren. Ganz zufrieden sind die Entwickler aber nicht. „Unser Problem ist noch die Achse“, verrät der Ingenieur. Im Testfahrzeug sitzt die integrierte E-Maschine hinten, vor der Markteinführung will ZF aber auf eine selbst entwickelte Mittelachse umsteigen. Auch das Gewicht von Motor und Batterie ist den Entwicklern noch zu hoch. „In der Summe wiegt das derzeit knapp eine Tonne“, sagt Hillbring. Eine Einsparmöglichkeit sei etwa die Größe der Batterie, die derzeit 70 Kilowattstunden speichern kann. „Damit könnte ich 60 Kilometer rein elektrisch fahren“, erläutert er und meint: „Wahrscheinlich würde auch eine Batterie mit 30 oder 40 Kilowattstunden reichen.“
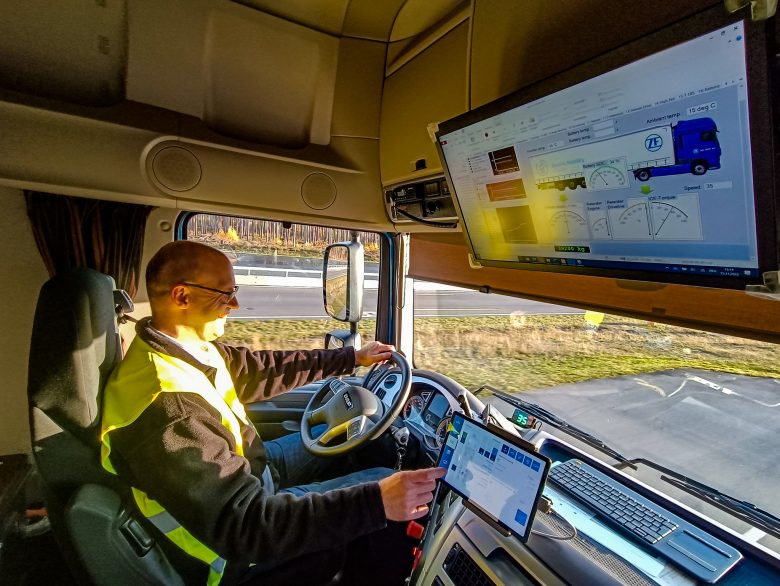
Während der E-Trailer noch viele Runden über die Erich-Reinecke-Testbahn bei Wietze drehen muss, hat das Friedrichshafener Unternehmen mit anderen Zukunftstechnologien schon Serienreife erreicht. Der kürzlich von ZF vorgestellte „Safety Innovation Truck“ kann eine autonome Notbremsung einleiten und das Fahrzeug noch vorm Aufprall zum Stillstand bringen – zumindest bei einer Höchstgeschwindigkeit von bis zu 80 Kilometer pro Stunde. Außerdem verfügt der Zukunftslastwagen über einen aktiven Sicherheitsgurt, der sich automatisch festzieht, sowie über einen Anfahrassistenten, einen Rückfahrassistenten und eine Totwinkelerkennung.
Nicht nur beim Umsatz, auch bei den Innovationen spielt der drittgrößte Automobilzulieferer der Welt inzwischen in einer Liga mit den Technologiekonzernen Bosch und Continental. Und genauso wie die Mitbewerber entwickelt sich auch der einst als Zahnradfabrik (ZF) für den Zeppelinbau gegründete Konzern zunehmend zum Systemlieferanten, bei dem sich die Kunden aus einem breiten Portfolio bedienen können. Ein zentraler Schritt dahin war die Übernahme des Nutzfahrzeug-Bremsenspezialisten Wabco, der neben dem Testgelände in Jeversen auch einige Fabriken sowie ein Technologie- und Innovationszentrum in Hannover in den Konzern miteingebracht hat.
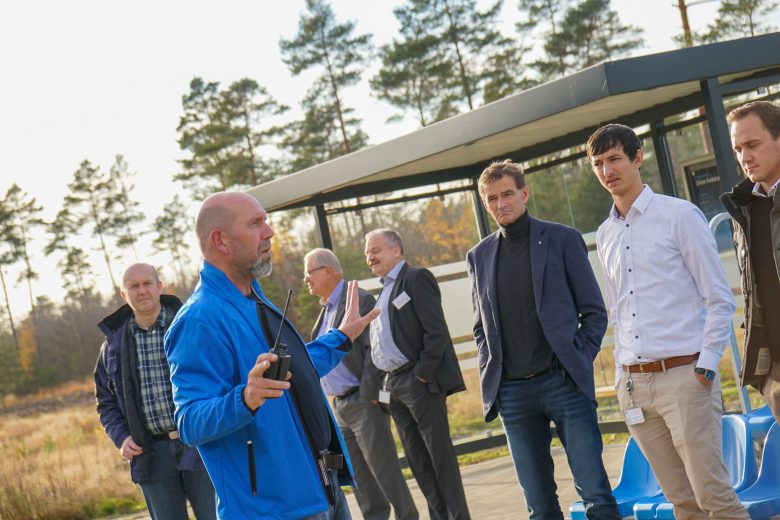
„Wir als Bremsenspezialist sind die optimale Ergänzung“, sagt auch Teststreckenleiter Henning Kutzner. Mit einer Gesamtfläche von 103 Hektar und acht Teststrecken ist das ZF-Testgelände zwar nicht ganz so groß wie das benachbarte Contidrom. Der hannoversche ZF-Chef Alexander Rohde betont aber selbstbewusst: „Es gibt in Deutschland keine vergleichbare Lastwagen-Teststrecke.“ Von der fünfspurigen Autobahn über Steilkurve, verschiedene Steigungen und regennasse Fahrbahnen bis zur Verladerampe können Kutzner & Co. hier alles nur Mögliche testen. „Wir haben hier Straßenbeläge von ganz glatt bis ganz griffig“, sagt Kutzner.
Besonders stolz ist er auf seine Autobahn-Schilderbrücke und die „Blaubasalt“-Strecke. „Das war früher mal die alte Braunschweiger Straße in Celle. Man hätte sie beinahe entsorgt, aber unsere Bauherren haben das Material gerne genommen“, berichtet der Teststreckenchef. Was ist so besonders daran? „Das ist eine natürlich gewachsene Straße, die im Lauf der Jahre glatt geschliffen wurde. Da sind schon Pferdekutschen drüber gerollt“, schwärmt Kutzner. Mit besonders viel Verve spricht er auch von der extra eingerichteten „bad road“ auf dem Testgelände. „Da kann man eine Achse mal richtig anregen und die Sensoren so richtig durchschütteln“, sagt der Teamleiter und räumt mit einem weitverbreiteten Missverständnis auf: „Eine schlechte Straße gut zu bauen, ist gar nicht so einfach.“
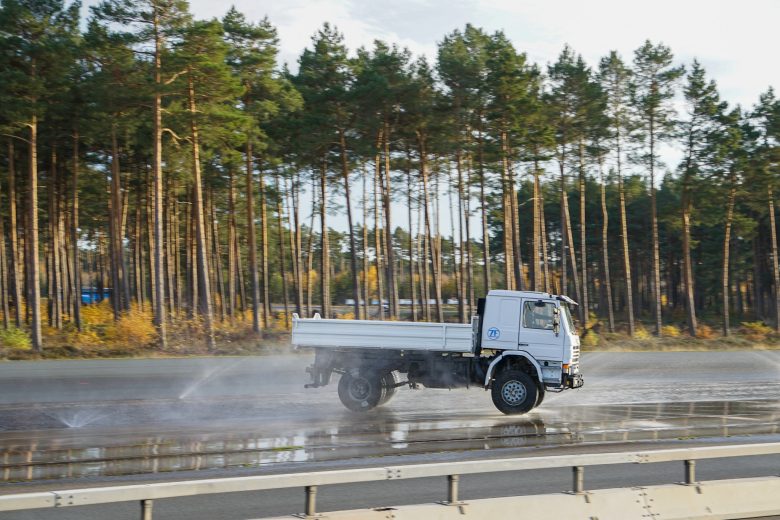
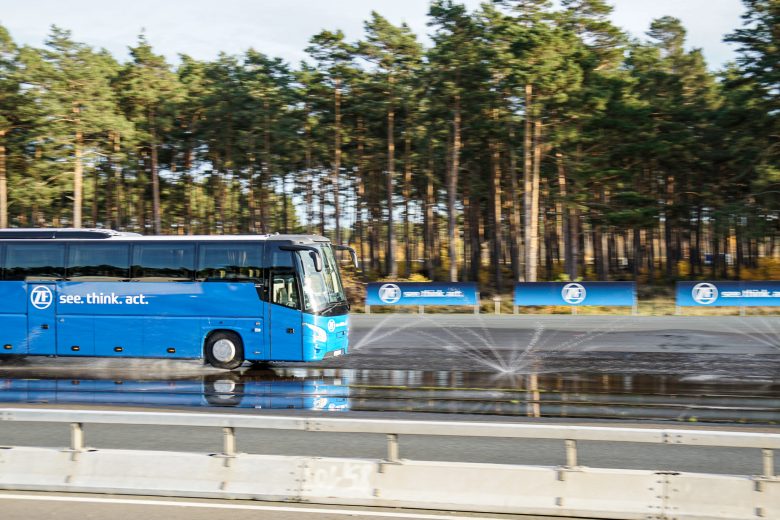
In den vergangenen Jahren hat ZF rund 20 Millionen Euro in die Erweiterung der Testbahn gesteckt. „Testen ist teuer“, weiß Kutzner. Dass die Probefahrt auf der Teststrecke in absehbarer Zeit durch Computersimulationen ersetzt werden kann, glaubt er jedoch nicht. „Das wurde uns schon vor zehn Jahren erzählt, aber es hat sich nicht bewahrheitet. Das letzte Prozent der Perfektionierung, für das der deutsche Maschinenbau berühmt ist, kommt nur durch den praktischen Test zustande“, sagt er und macht sich keine Zukunftssorgen. „Es wird genügend Arbeit geben.“
Die nächste Erweiterung ist sogar schon geplant. Das Projektcenter soll um einen Anbau für noch mehr Büros und Meetingräume ergänzt werden, weil es für die insgesamt 250 Zugangsberechtigten eng wird. Und auch der Parkplatz reicht schon längst nicht mehr für die vielen verschiedenen Fahrzeuge aus, die täglich in Jeversen getestet werden. Damit die Assistenzsysteme auch überall funktionieren, müssen sie nicht nur in Lastwagen oder Bus, sondern auch in Sattelschlepper oder Betonmischer getestet werden.
Kutzner: „Ich habe hier von Tag zu Tag auch immer mehr elektrifizierte Fahrzeuge. Das macht nicht bei den Autos halt, sondern betrifft auch die Nutzfahrzeuge.“ Nur eins kann die Testanlage nicht: Winterbedingungen mit Schnee und Eis simulieren. Dafür mietet sich ZF regelmäßig bei einer finnischen Teststrecke am Polarkreis ein.
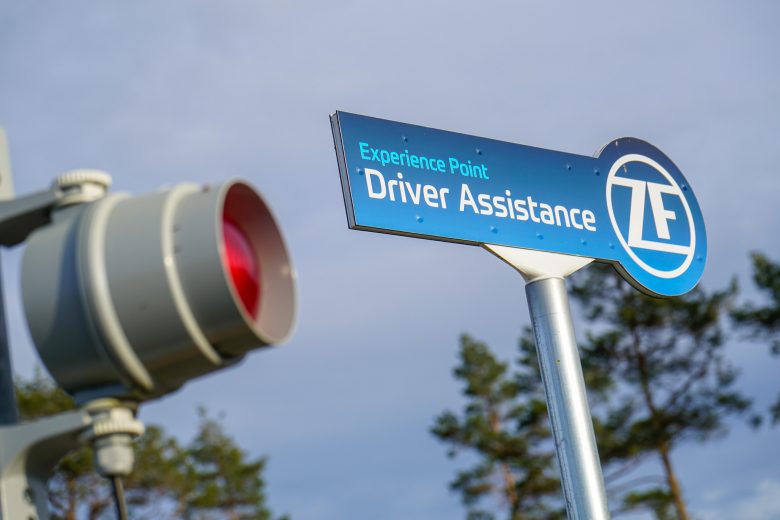
Während in der Automotive-Branche derzeit viele Unternehmen schwächeln, hat ZF auch 2021 seine Jahresziele erreicht. Der Umsatz lag mit 38,3 Milliarden Euro deutlich über dem Vorjahresergebnis (plus 17,5 Prozent). Davon werden etwa eine Milliarde Euro von den 3000 ZF-Mitarbeitern in Hannover erwirtschaftet, sagt Rohde. Künftig sollen die etwa 800 Entwickler am Lindener Hafen sogar noch 220 neue Kollegen bekommen. „80 haben wir schon an Bord“, sagt Rohde und ist zuversichtlich, dass er auch die übrigen Stellen besetzen kann. „Der Name ZF hilft. Wir sind der Vorreiter beim autonomen Fahren im Nutzfahrzeugbereich“, sagt der frühere Wabco-Manager und verrät auch das ZF-Erfolgsmodell: „Wir verbinden Mechanik, Elektronik und Software miteinander.
Dieser Dreiklang wird immer wichtiger.“ Wie bei allen Unternehmern ist auch bei ihm die Energiekrise derzeit das drängendste Problem. „Wir selbst haben gar nicht so hohe Energiekosten, aber auch wir brauchen Metall“, sagt Rohde und sorgt sich vor allem um die kleineren Zuliefererbetriebe. Von der neuen Landesregierung fordert er deswegen vor allem eines: „Der Industriestandort Niedersachsen muss stabil bleiben. Das Land hängt am Tropf der Automobilindustrie.“ Beim neuen Wirtschaftsminister liegt diese Aufgabe aus Sicht des ZF-Managers jedoch in guten Händen. „Olaf Lies kennt das Thema“, sagt Rohde lakonisch.
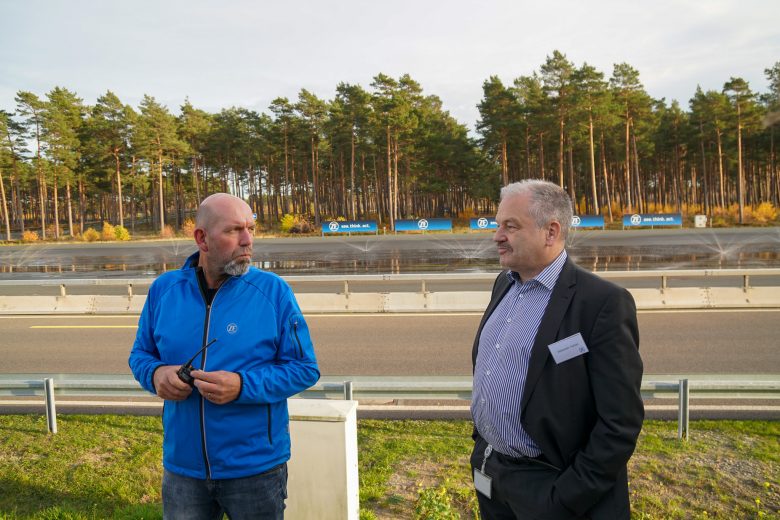
auf die ZF-Teststrecke bei Jeversen im Landkreis Celle. | Foto: Link